The food industry is looking for a better balance between functionality and costs. The easiest way is also to choose the right system for handling raw materials, semi-finished and finished products.
Operations in the food industry rely on an efficient handling of materials. Production and safety of products also depend significantly on the transport within the plant of: Raw materials, semi-finished and finished products. Making the most of internal handling means eliminating unnecessary and wasted time. The firm must identify the best possible path and use the most appropriate tools. The basic principles of interior handling systems were developed at the beginning of the last century.
Innovation is the result of automation, computer technology and the development of electronics. The traditional control system used the “action-reaction” principle. It used proximity sensors or photocells placed on the conveyor belt and few other status information sent by conveyor systems downstream. Early sensors installed on production lines, for instance, controlled the automatic systems for centering conveyor belts. This principle is still used, and sensors control the position of the belt edge.
The signal is sent to the control roller which, if necessary, repositions the belt correctly. The risks of inefficiency grew as plants grew more complex. New technologies allowed the connection between the sensors supplied with the systems and the sensors of other machines. Thus, the system can monitor the entire production line and adjust its operation according to the data collected.
Internal product handling
Material handling on food production lines can account for up to 80% of the firm’s activity and up to 50% of its operating costs, even if it does not add value to the production process. Flexible and efficient systems are essential, designed with the classic questions in mind: What needs to be handled? When, where and how to do it? Who does it? The design of internal handling follows three basic principles: Standardization, modularity, and flexibility.
The chosen solution must cover as many activities as possible, operate in the different environmental conditions of the firm, ensure safety with little or zero operational interventions, must not waste product or contaminate the work area. Other important aspects are the reduction of energy consumption by exploiting the force of gravity as much as possible, a rational utilization of the available space vertically, horizontally or in a mixed direction. The system must be designed to manage the desirable firm growth, avoiding new and costly investments.
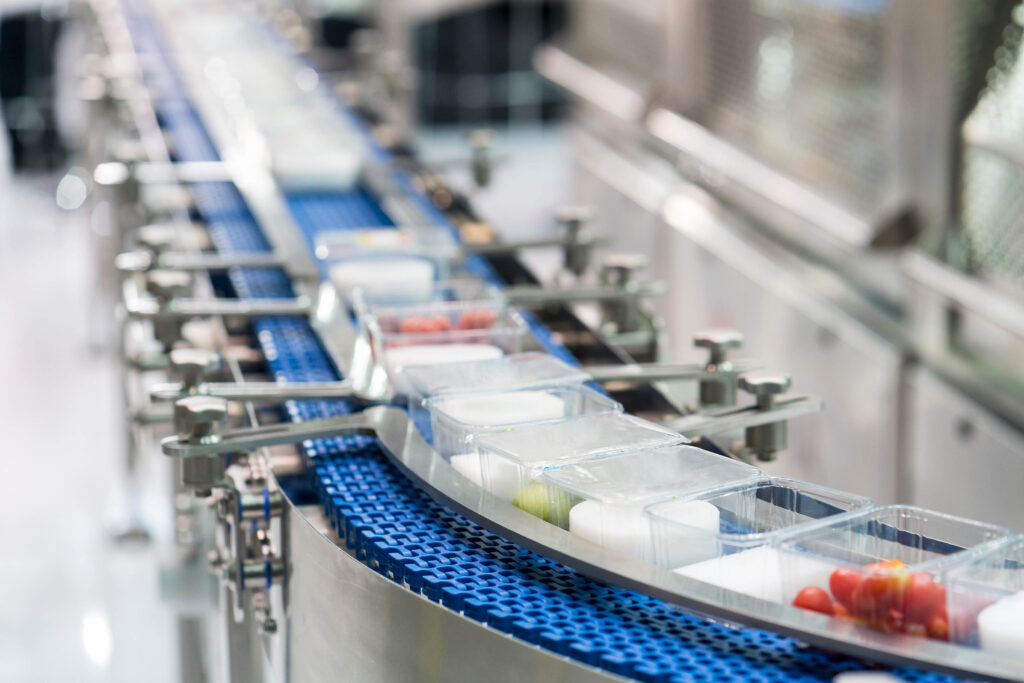
Conveyor belts
Conveyor belts are one of the most popular solutions: They can be loading, linking, or bypassing belts; they are used to connect or divert raw materials, semi-finished or finished products from one production step to the next. These are general product conveyance applications, aligning and transferring products in bulk or in trays; removing washing water; entering/exiting an oven or freezer; belts used for sorting fruit and vegetables or other products prior to packaging. Operators are in charge with the elimination of scraps on manual sorting belts.
Automatic sorting systems use different principles. Waste separation can be done by compressed air, because the compliant product and the waste have a different weight. Selection can also be done according to their different density, or according to their different colour, using more advanced optical sorting systems. The conveyor is formed by an AISI 304 or aluminium alloy frame; a belt running on a plane or on rollers; a motor; a return roller usually placed at the end of the frame.
The most common add-ons are drive and tension assemblies, belt centering systems, product deviators or accumulators, and sensors. The belt can be flat or concave, i.e. supported by pairs of V-shaped sliding rollers. Today, there are different types of conveyor belts designed for a specific application. For example, a high level of hygiene is ensured by belts with long-lasting antimicrobial and anti-biofilm effects (ISO 22196).
There are belts with high resistance to oils and greases, or with characteristics of low capillarity (Wicking Test G11-FDA 2011), resistant to cracks, cuts, and abrasions. There are also belts which, although subject to large thermal fluctuations, retain great flexibility; and high-strength plastic mesh belts for washing and transporting vegetables, fruit and frozen foods, as well as for draining liquids and sorting solid residues.
Some technical features
Metal structures should not deform due to product weight, belt tension, and uneven flooring. The metal parts that support antistatic belts must have a “ground” connection to discharge the electrostatic potential accumulated by the belts themselves. Supporting the belt with a sliding plane achieves good stability of the conveyed products, and less non-conformities in the event of inaccurate belt centering. The belt also has the possibility of oscillating transversally.
The material of the sliding belt influences the friction coefficient of the belt/plane, limits, or enhances the noise of the system, reduces, or increases the belt wear. The sliding plane must be aligned with the belt and have rounded edges. The entire structure must be regularly cleaned to prevent increased friction coefficients and premature belt wear. In inclined conveyors, ribbed belts or profiles on the bearing surface are used to prevent the conveyed product from backing up or falling. The most suitable type and height are determined depending on the characteristics of the conveyed material and the inclination angle of the conveyor belt.
Rollertrack conveyor
If the runway is long and the loads are heavy, the sliding plane can be replaced by a rollertrack. This solution reduces friction, peripheral force and the pulling power. The conveyed products move in the opposite direction to the driving belt/chain. In presence of considerable loads, e.g. plastic boxes used for sanitizing fruit and vegetables, the distance between the rollers must be less than half the length of the loading units. Only in this way each load unit rests on at least two rollers.
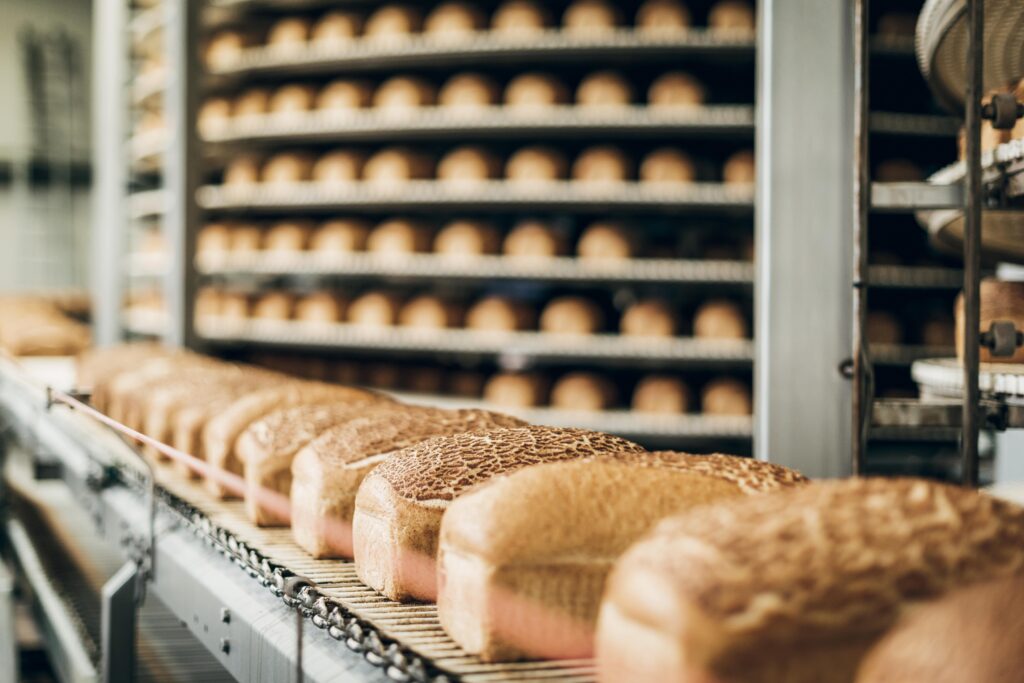
Some critical phases
产品装货期间,受到皮带mechanical stress resulting from the impact between the product that falls onto the belt and the belt itself, as well as from the reciprocal movement between these two system components. In order to have the least impact in the movement direction of the belt, it is a common rule to load the material as far as possible in the center of the belt. If the path involves a lateral deviation of part of the product, rigid orientable deviators, deviators with power-driven discharge belts, right-angle side deviators, or movable deviators are installed, as appropriate.
In each of these cases, deviators and belts must not come into contact, and the transverse forces exerted on the belt shall be limited. If the conveyor moves upwards, the belt towing is at the beginning of the system; if it moves downwards, the tail towing is preferable, because, if necessary, it can act as a brake. The maximum level difference depends on the weight of the products, their structural characteristics, the surface finish, the operating conditions of the conveyor belt (speed, run/stop, vibration), and the environmental conditions (humidity, temperature, dirt).
In case of curved sections, the turning angles may be between 30° and 180°. In curves, the conveyed products hold their position, but the curve generates high transverse forces that pull the belt toward the center point of the curve. These forces must be absorbed by the metal elements of the conveyor. In some applications, it is preferable to replace a single large belt with a series of narrower belts that run parallel to each other. Coarse impurities fall between belts and are immediately separated from the conveyed products. In addition, in very humid or wet products, the excess water flows out during handling.
Troughed conveyors
Some bulk products require the use of trough conveyors. The belt support in the loading area consists of two or more sets of rollers or a troughed conveying plane. In the loading area, the degree of curvature of the belt under load shall not exceed 1 per cent of the center distance between the support rollers. The speed is adjusted to minimize product loss. For example, for bulk grain conveyance, industry experts recommend an average belt speed of 2.5 to 2.8 m/s, but never more than 3.5 m/s. Equipment costs typically decrease as distances grow.
Bucket Elevator
When horizontal spaces are small, bucket elevators are preferred, which are suitable for moving granules or powders at different heights. The conveying speed is calculated on the basis of the characteristics of the products being processed, the duration of their storage and the risk that, in the case of cereals, they may fall apart during that period.
A bucket elevator consists of buckets attached to a chain or belt that revolve around two sheaves, one at the top and the other at the bottom. Depending on the conveying needs and chemical characteristics of the product being handled, the buckets can be made of steel (carbon, wear-resistant, stainless) or plastic. In the food industry, the bucket elevator is used for grain transport and, in general, for the height transfer of bulk products to be stored or used in production.
产品装入移动你的桶pwards and is released by gravity or centrifugal force. The system capacity is due to the speed of the chain / belt and the number of buckets per meter. The length of the elevator can range from a few meters to more than 50 meters. Bucket elevators have capacities ranging from 2 to 1000 t/h. Different configurations are possible, depending on whether the loading and unloading are on the same side or opposite sides of the machine.
If the buckets are facing the same way, they fill with product at the bottom of the machine; conversely, if the loading and unloading are on opposite sides, the buckets are gravity-filled directly from the loading hopper. Elevators of the latest generation are equipped with inductive sensors with an anti-belt mistracking function: The sensors allow the tracking of the belt within the running space to be monitored, and any abnormal lateral mistracking of the belt to be detected. The generated signal can be used as an alarm or as an input to an additional safety system that stops the machine.
Scroll conveyors
Scroll conveyors are continuous conveyors used for the conveyance and lifting of loose materials, in small pieces or in powder, often for loading and unloading from silos. The propeller can be with one or two principles, constant pitch, increasing pitch for better material dosing, decreasing pitch to compress the material in case of pressure vessels other than ambient.
This system is typically used for short distances, costing less than a belt system of the same length and capacity. Scrolls are low maintenance, completely closed and therefore provide a tight seal against dust. Another important advantage is their simple construction. The choice of materials and sizing of all components are adjusted from time to time according to the characteristics of the product to be treated (abrasion, pile weight, particle size, moisture, aggressive chemicals). Carbon steel or stainless steel are commonly used for scroll construction.
Pneumatic Conveyor
气动运输发生在封闭的管道s. It is used when space is relatively limited or when material must be transferred by aspiration from multiple sources and directed to a single destination. Only materials with very low humidity are transported. The motion of the material is obtained by means of a current of air in depression (in aspiration) or pressure (in thrust) in the piping. Air is usually used for conveying materials or, depending on requirements, a different gas, such as nitrogen, can be used, which being inert lends itself for transporting potentially explosive materials.
The gas can be handled by a pump, a blower, or a suction unit. The air pressure on the line is determined by the device that manages it and generates the pressure or vacuum. If the device is positioned at the beginning of the line, the line works under pressure; if it is positioned at the end of the line, the line works under vacuum. The parameters vary mainly according to flow characteristics, grain size, specific weight of the product that must be conveyed, the profile of the conveying line (pressure drop) and the desired performance.
The material can be moved continuously or in batches. If the material is transported in suspension in the air, the transport is known as dilute phase transport (usually non-abrasive powders or granules) without flowing along the inner wall of the tubes. If the material is moved at low speed, not in suspension, through the whole tube, the transport is known as dense phase transport.
Dense phase transport is characterized by a high product-to-air efficiency ratio (30 liters of carrier gas per 1 kg of product). The low transport speed preserves the quality and integrity of any type of material: Fragile, abrasive, delicate, mixed or tending to agglomerate. The transport is in semi-dense phase when the air velocity is lower than that of dilute and dense phase systems, with specific intermediate pressures and product-to-air ratios.